Product
Electronics
AGV/AMR
AGV/AMR
- Customized AGV system based on accuracy and reliability
- User interface design for easy use by field workers
- Production management system integration
- Autonomous charging and AGV multi-control implementation
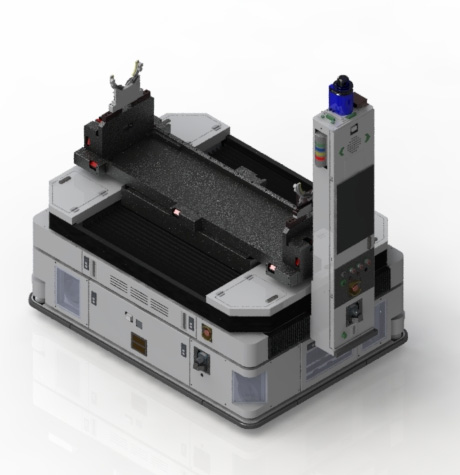
Features
- - Efficient replacement of repetitive logistics transport
- - Real-time logistics flow control and accurate logistics transport via flexible system operation
- - Logistics transport manpower reduction and productivity improvement
- - Pursuit of comfortable working environment through diversification of on-board device (transport device)
- - Safety accident prevention through triple safety devices
Specification
[Classification by guiding method]
1.
MGV (Magnetic Guide Vehicle)
- Buries magnets or affixes magnet tape on the floor
to guide using a magnetic guide sensor.
- Buries spots (iron plates, magnets) in the floor
at certain intervals to guide/control AGV positions using a guide sensor.
- Easy to install and operate and has low
construction costs.
2. Optical
Guidance
- Guides AGV with a PGV sensor by attaching colored
tape or QR code to the floor.
- High-precision and easy to control traffic.
3. LGV
(Laser Guide Vehicle)
- Guides with a laser scanner using AGV's absolute
coordinates after installing a high-brightness reflector.
- Enables high-precision driving.
- Track can be changed and expanded wherever an
LGV-recognized reflector is attached.
4. SLAM
(Simultaneous Localization and Mapping)
- Guides driving by recognizing images of terrain
using surrounding terrain, installing random terrain, or laser distance.
- Easy to create a new map even with frequent
changes in the location of facilities.
[Classification by driving method]
1. SD
(Single Driver) Type
- General AGV driving method.
- Driving and steering motors are assembled in one
configuration (dedicated AGV wheels).
- Guiding baseline is located at the center of the
driving part, and the control moves along the baseline.
2. DD (Dual
Driver) Type
- Steering control uses the speed difference between
two motors.
- Easy to spin/turn and move backward.
- Has a stable structure for handling high-load
cargo.
- High steering control skill is required with the
implementation of the speed deviation-based steering, which is a typical AGV
driving method.
3. QD
(Quad Driver) Type
- Drives individually by arranging the SE-type
motors front and back (left, right).
- AGV can transfer and load cargo immediately after
making a sharp curve.
- Zigzag driving is possible.
- Stable when loading up to 6,000 kg.
- Dual driving requires high-control skills.